Parts reconditioning
Solenoid valves, cylinders, shock absorbers, PCBs… BMR reconditions any type of parts used in glass bottling factories.
Let’s work together
Contact us by mail or by phone for more information
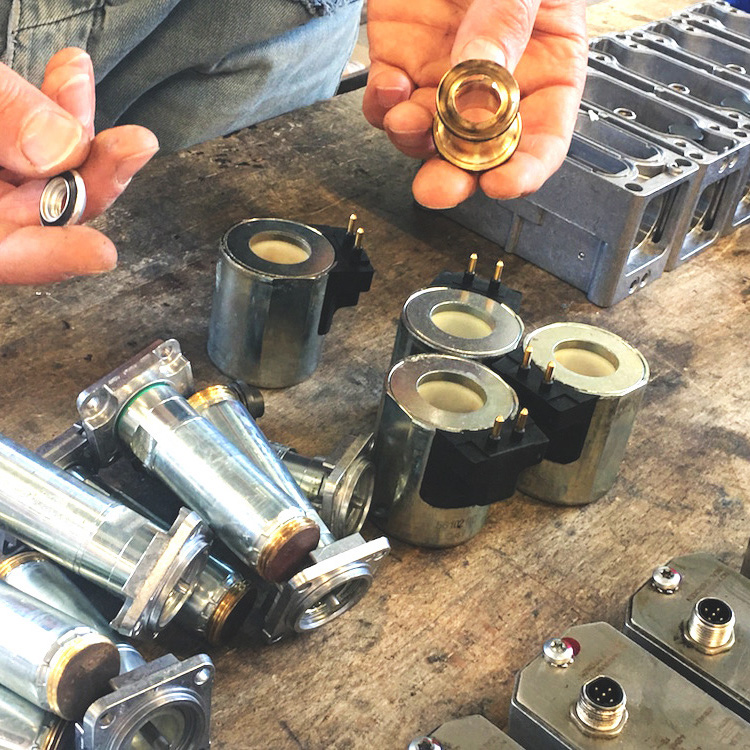
Why reconditioning?
Reconditioning a part might seem to be useless. Why not just buy the same new part instead? Well, reconditioning parts does have its shares of advantages, beginning with direct and indirect costs savings.
Benefits of the reconditioning
Flat rates for repair generally vary between ½ to ⅕ of the price if the parts are new.
This package is to be considered when you first come into our workshops.
Once repaired at least one in our workshops, the additional maintenance by parts is no longer based on the flat rates but on the real costs.
As BMR has access to every spare part from different manufacturers, a part may have a cost of repair divided by 3 until approx. 25€ excl. taxes (Depending on what components need to be changed).
The maximum cost of repair can’t exceed ⅔ of the price of the new. If the cost surpasses ⅔, we advise to change the part without any additional billing.
Please note: Once that, after a first inspection, a part has been identified as unrepairable, this one is considered as such and won’t be charged.
Inside our package is included rigorous inspections of the parts before, during, and after the intervention of our team.
The validated parts will have performance and tilt safety margin close to new ones.
This rigor allows us to ensure the reassembly of the reliable and performing reconditioned parts on the machines.
During the reconditioning, the parts go in our workshops to be engraved with two letters corresponding to which factory they come from, followed by the number of the repaired part.
All the references, the notes before and after reconditioning, the values and customer data (summary customer file indicating the exact location of the part assembly, the date, the hour, the team that changed the part and the reason why) are classified on an Excel file.
This file is provided with the repaired part delivery bill as well as with the actual computer excel file sent by email.
When a part comes back in our workshops, the repair history and the precedent operation notes are considered to determine the relevance of the additional repair or of a component being put aside.
This allows to avoid any reinstallation on a machine of components where doubt would still subsist concerning their reliability, and to limit incurred shutdowns.
Some parts or pilots have delivery lead times that can take up to 10 weeks. This, plus the fact that many factories use the same solenoid parts and pilot references can lead to difficult section shut down situations.
Example: Depending on the manufacturer, PPEs are not repairable as their valves are crimped inside their bodies.
However, BMR is equipped to recondition and test those parts and pilots used in glass factories.
Our package includes:
- Reception
- Inspection and control
- Cleaning
- A follow-up engraving
- Disassembly
- Replacing all the parts included inside the repair kit
- Reassembly
- Tests (pneumatic, electric)
- A traceability file